HSK工具系統的選用
時間:2024-04-09 16:14:05 來源:admin 點擊:0次
在高速切削加工中,根據加工要求正確、合理地選用HSK刀柄十分重要。在選擇HSK刀柄的型號和規格時,主要的考慮因素包括:主軸的最高轉速、刀柄的結構特點和承載能力、刀具及配套件的普及程度等。
A型有傳動槽,相對來說A型傳遞扭矩較大,可進行一些重切削。A型刀柄除有傳動槽之外,還有手動固定孔、方向槽等,則比較來說平衡性較差。所以轉速就相對較低,可在主軸轉速為20000~30000r/min的機床上使用。E型沒有傳動槽,傳動的扭矩就比較小,只能進行一些輕切削。而且也沒有手動固定孔、方向槽等,屬于固有對稱型,所以E型更適合于高速加工。F型和E型的區別在于:同樣標號的F型和E型刀柄(比如F63和E63),F型刀柄的錐部要小一號。也就是說F63和E63的法蘭直徑都是φ63mm,但F63的錐部尺寸只和E50的尺寸一樣。所以F63和E63相比,其主軸軸承小,轉速要更快些。HSK工具系統的6種規格及其應用領域如表所示。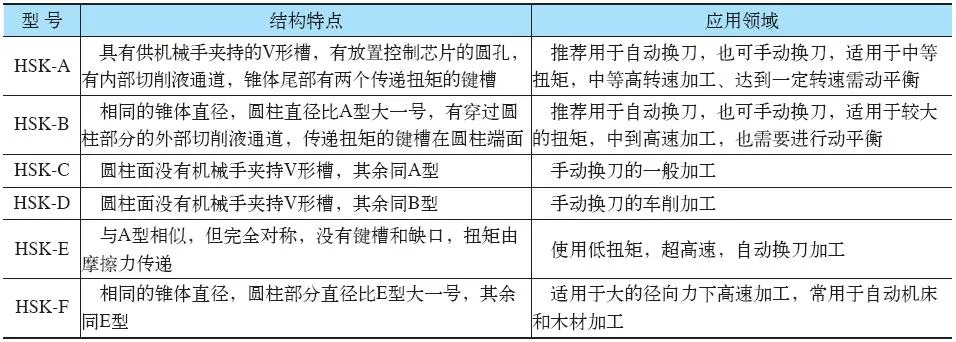
(1)刀柄型號的選擇。由HSK刀柄的結構特點可知,A、B型刀柄主要用于帶有自動換刀裝置機床的中高速加工;C、D型刀柄主要用于采用手動換刀的中高速加工;而E、F型刀柄由于無任何槽和切口的對稱結構,動平衡性較好,因此適用于超高速加工。國內采用DIN6989b-1中的A型和C型標準,如HSK50A、HSK63A、HSK100A等。HSK50和HSK63刀柄的主軸轉速可達25000r/min,HSK100刀柄可12000r/min,精密平衡后的HSK刀柄可達40000r/min。隨著轉速增加,徑向剛度將有所降低。下圖為HSK與BT錐柄主軸轉速與徑向剛度關系的比較。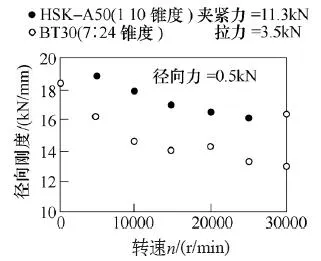
(2)刀柄規格的選擇。選擇HSK刀柄規格時,主要應考慮刀柄的承載能力(包括極限彎矩和極限扭矩),應根據實際加工時切削力產生的彎矩和扭矩,而承載彎矩的能力與夾緊力有關,實際上刀柄上承受的彎矩是由橫向作用在刀具上的力產生的。刀柄的彎矩承載能力是在彎矩作用下,使刀柄法蘭接觸面的一邊開始分離時的彎矩值,從這個臨界彎矩值開始,彎矩-變形特征曲線的走向明顯變陡,表明刀柄裝夾的連接強度迅速降低。在接近臨界點時,連接強度已經不夠,盡管此時刀柄的法蘭面與主軸端面還保持全面接觸,但彎矩已接近使兩者分離的臨界值。這個臨界彎矩的大小主要取決于拉緊力,因此加大拉緊力可以提高最大彎矩。這一點對懸伸較長的刀具有特殊的意義,此時一個較小的切削力就會產生較大的彎矩。但是加大拉緊力會增加作用在刀柄夾緊斜面上的總載荷,尤其是在高使用轉速下,由于離心力的作用,內部夾爪所施加的夾緊力隨之增加,致使夾緊的可靠性得以提高,但另一方面卻使刀柄最薄的部位承受很大的載荷,導致刀柄損壞。損壞扭矩的大小與材料密切相關。如能正確選用材料,則可明顯提高刀柄的承載能力。為了確定刀柄的最大扭矩承載能力,僅做靜態試驗還不夠,在切削加工中所產生的動態激振的持續作用下,刀柄承受扭矩的能力明顯下降。對于所有的材料動態承載能力大的只有靜態試驗時的7%。下面僅以HSK-63型刀柄為例對各種規格的HSK刀柄進行比較。1)HSK-63A-C型刀柄夾緊力:15kN,18kN,21kN。2)法蘭端面分離彎矩:420Nm,460Nm,510Nm。3)滑動扭矩:115~155Nm,138~186Nm,161~218Nm。4)靜態試驗破壞扭矩:2200Nm(16MnCr5,56HRC),2400Nm(41Cr4,53HRC),3300Nm(X46Cr13,53HRC)。5)動態試驗破壞扭矩:1600Nm(16MnCr5,56HRC),1800Nm(41Cr4,53HRC),2400Nm(X46Cr13,53HRC)。6)最高使用轉速:22500r/min(最小過盈配合),27500r/min(最大過盈配合)。對于E型結構(不帶鍵槽)的HSK刀柄,可傳遞的最大扭矩是靠刀柄與主軸之間的摩擦實現的,其大小除與錐度配合精度之差有關外,還取決于拉緊力。一個HSK63號刀柄的滑動扭矩在按照DIN標準推薦的18KN拉緊力情況下為138~186Nm,如果把拉緊力提高到21kN,滑動扭矩大約可提高20%,達161~218Nm。具體選擇時可查閱相關手冊,根據其所列的極限彎矩和極限扭矩來選擇刀柄規格。下表為HSK刀柄的規格分布。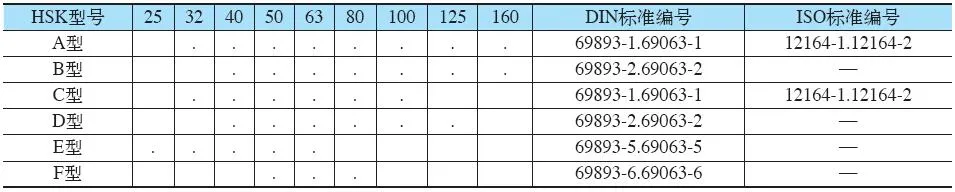
目前使用最廣泛的是HSK-A型,大約占總量的98%,HSK-A型刀柄如圖所示。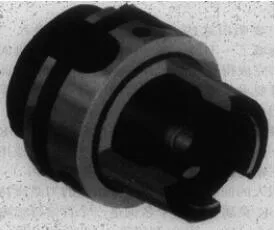